Sheet piles can be classified into various types based on the form of their cross-sections:
U-shaped pile: The surface of the board presents a "U" shape and is interlocked through the locking clips at the edges, thus forming a continuous wall. The wall thickness distribution of U-shaped piles is uniform, but the moment of inertia of the cross-section is slightly lower than that of Z-shaped piles of the same specification.
Z-shaped pile: The plate surface presents a "Z" shape, with a serrated appearance. The interlocking structure is far from the neutral axis, featuring good cross-sectional rigidity and convenient interlocking. It is often used in port construction and deep foundation engineering applications. Its application scope is more extensive than that of U-shaped piles.
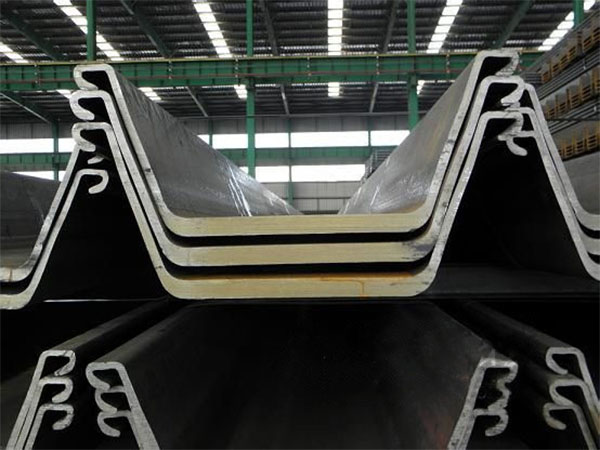
Materials and Specifications
Different materials can offer different properties and characteristics. As structural components, sheet piles typically use carbon steel, low alloy high strength steel, as well as high galvanized and stainless steel materials that are resistant to seawater corrosion.
Wall thickness range: generally 4 mm to 12 mm. Different specifications can be customized to be thicker or thinner according to engineering requirements.
Length and width: Standard lengths are 6 m, 9 m, and 12 m. They can also be spliced according to the on-site terrain, water depth or enclosure height. The width of a single piece is usually 300 mm to 600 mm.
Production and manufacturing processes
The main production processes of steel sheet piles are cold bending and hot rolling. The cold bending process involves gradually bending the steel sheet through a cold bending forming machine, while the hot rolling process involves heating the steel billet and rolling it on a rolling mill. The following are the main process steps:
Cold bending process: uncoiling → leveling → butt welding → forming → finishing → straightening → sawing. It is suitable for thin-walled and small-section pile types and has a relatively low cost.
Hot rolling process: heating → rough rolling → finish rolling → shaping → cooling and straightening → cutting and surface treatment. The parameters of the hot rolling process are extremely demanding, requiring precise control of temperature, speed, pressure and other parameters. Hot-rolled formed sheet piles have high cross-sectional accuracy and good cross-sectional performance.
The driving method of sheet piles
Individual driving method: Start from one corner of the board wall and drive each piece one by one until the project is completed. Its advantages are convenient and rapid construction and no need for other auxiliary supports. The drawback is that it is prone to causing the sheet piles to tilt to one side, and as the sheet piles continue to be driven in, the tilt will become more obvious and difficult to correct.
Screen-type driving method: It involves inserting 10 to 20 steel sheet piles in rows into the guide frame in a screen-like shape, and then driving them in batches. When driving, first drive the steel sheet piles at both ends of the screen wall to the designed elevation or a certain depth to form positioning sheet piles, and then drive them in the middle in a stepped manner at 1/3 and 1/2 of the sheet pile height in sequence. The advantages of the screen-type driving method are: it can reduce the accumulation of inclination errors, prevent excessive inclination, and is easy to achieve a closed closure, which can ensure the construction quality of the sheet pile wall. Its disadvantages are: the self-standing height of the pile driving is relatively large, and attention should be paid to the stability of the pile driving and construction safety.
Entry method
Vibrating pile driving: Use a vibrating hammer to quickly insert, suitable for loose soil layers; However, it is not suitable for hard soil or areas with high noise restrictions.
Static pressure installation: Utilizing a hydraulic static press to apply force and slowly press in, it features low noise and minimal disturbance, making it suitable for urban areas and environments with high environmental protection requirements.
Rotary drilling: Drill holes first and then drive sheet piles. It is suitable for geological conditions with many underground obstacles or soft and hard interlayers.
Concrete pouring: By integrating the cast-in-place pile technology, pouring holes are arranged in front of and behind the sheet piles to enhance the stability of the retaining structure.
Application field
Retaining and support: Slope support along highways, railways and Bridges.
Cofferdams and temporary support: port terminals, foundation pit excavation, river course management.
Moisture-proof embankments: Coastal moisture-proof walls, river embankment reinforcement.
Underground continuous wall auxiliary: Serves as a temporary support on the outside of the continuous wall.
The grade standard of sheet piles refers to the ASTM standard. Its basic grade is ASTM A572 Gr 50, and ASTM A690 and A588 can also be used. ASTM A690 can reduce the corrosion rate in the splash zone by 2 to 3 times, and A588 has the characteristic of resisting atmospheric corrosion.
Summary
Steel sheet piles, with their features of convenient construction, reusability and remarkable support effect, have become an important structural form in modern civil engineering fields such as foundation pit support, retaining and cofferdam. Selecting the appropriate pile type, material and installation process, combined with reliable design calculation and anti-corrosion maintenance, can ensure the safety and economy of the project.
Read more: Steel pipe pile or Difference between pipe pile and sheet pile?