1. Porosity
Porosity is the most common welding defect, which is formed by the inability of the gas in the weld to be completely released during the solidification process. Porosity will reduce the strength and sealing performance of the weld, and even cause the weld to rupture.
2. Slag inclusion
Slag inclusion is the failure to completely remove foreign matter such as impurities and oxides during welding, resulting in these impurities being sandwiched inside the weld. Slag inclusion will reduce the strength and sealing performance of the weld.
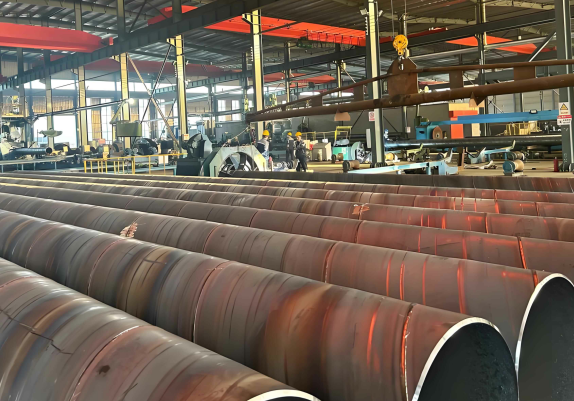
3. Cracks
During the welding process, cracks may appear in the weld due to the effect of thermal stress or other reasons. Cracks can cause the weld to break and reduce the strength and sealing performance of the weld.
4. Welding residual stress
During the welding process, thermal stress can cause certain residual stresses in the weld and the base material. This stress can affect the deformation and performance of the welded parts.
5. Pinholes
Pinholes are tiny pores that usually do not have a significant effect on the strength and sealing performance of the weld. However, when the pinhole density is large, the strength of the weld may be reduced.
6. Welding temperature is too high or too low
During the welding process, if the temperature is too high or too low, the weld may not be completely melted or melted unevenly, affecting the quality of the weld.
7. Weld deviation
The phenomenon that the weld deviates from the design position is called weld deviation. Weld deviation will affect the strength and sealing performance of the welded joint.
8. Unqualified weld size
If the weld size is too large or too small, the strength and sealing performance of the welded joint will be reduced.
9. Loose weld joint
The welded joint is not well combined, resulting in loose welds and low strength.
10. Welded joint is not firm
Failed to achieve sufficient welding strength during welding, and the joint is easy to loosen or fall off.
11. Welding deformation
During the welding process, the size or shape of the welded joint changes due to deformation caused by thermal expansion.
12. Uneven weld surface
During the welding process, the weld surface cannot be flattened, which affects the appearance and use effect.
The above are common welding defects of ERW steel pipes. These defects will have a negative impact on the strength, sealing and durability of the welded pipes. Therefore, welding operators should strictly control welding parameters, check weld quality, and deal with welding defects in time during the welding process to ensure the quality and reliability of the welded joints.
Read more: SAW vs ERW and EFW Welded Steel Pipe or Seamless pipe vs Welded pipe Price